EnviroAir designs custom wet scrubber systems including packed bed scrubbers. Our specialty is turnkey installations of environmental air systems and can provide single source responsibility for the design, fabrication, installation and startup of your wet scrubber system. Packed towers or packed bed scrubbers are essentially contact beds through which gases and liquid pass counter currently or cross flow. They are used primarily for applications involving extreme pH gases, odors, vapors, and mist removal. While these collectors can capture solids, they are not normally used for this purpose because wet dust collecting in the beds would require unreasonable maintenance.
Packed bed scrubbers are designed to neutralize gases and odors produced during manufacturing processes. Usually, the flow through a packed bed scrubber is counter current, the liquid is introduced at the top and flows down through the packing, while gas is introduced at the bottom to flow upward through the packing. The packing is designed to produce a large surface area for the liquid to contact the solute gas. The countercurrent flow is highly efficient since, as the concentration of pollutant in the gas decreases while rising through the tower, there is a constantly fresher neutralization liquid available for contact.
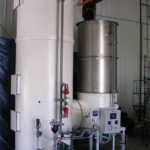
Optional Packages
EnviroAir utilizes pH controls, flow meters, ORP controls, and conductivity controls to provide a system with highly efficient gas treatment and maximum user flexibility. Often, a simple change of feed chemical is all that is needed to accommodate a change in process gas. Optional packages include high temperature quench sections, multiple stage designs, and horizontal profile scrubbers.